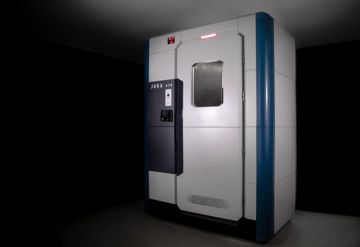
Industrial design
Sheet metal housing for access control x-ray machine
Sheet metal housing for access control x-ray machine
EasyFill Multitool - The product was featured on Suzelle DIY Simply scoop it, scrape it, sand it and seal it! Watch the EASYFILL Advert
I work with 112Motion, a team of skilled profesionals located around the world. We design medical wearables and accesories which leverage the latest in cloud based technology, global positioning systems and bio sensors to create devices which improve the lives of the elderly.
Polo cup racing livery for Repro Supplies.
CNC milling a plug for a series of container prototypes.
Rapid prototype bottles printed in clear green resin.
Rendering of xray housing before production.
Model JS1 glider assembly for tooling pattern development.
A retro styled wheel design for Dutchmann Porsche
Early concept drawing for CareWatch wearable fall prevention device.
The development of Unmanned Aerial Vehicles over the past few years has been astonishing. I have been fortunate enough to style a few of them, the one pictured here is the Elevation VTOL by Avior Labs.
This robot toy was designed entirely in South Africa and blurs the lines between board games, radio control vehicles and online first person shooters.
A new pack design for Lonza chemicals for their weekly dosing system. After presenting a range of revolutionary concepts it was decided to leverage their recognisable chlorine bottle shape, in a smaller size tailored to the new system.
This headlamp is a great example of the end to end Industrial design solution I offer. The working prototype pictured here started out as a series of concept drawings which where refined into to workable design. The prototype was printed from the final CAD drawings and was then tested in real world conditions. Any snags which were identified were resolved before going into production.
For organic shapes and detailed assemblies, digital 3D scanning is an absolute game changer.
Multitool test prototypes shown with the first off production unit (top).
The acrylic stars were assembled from simple 2D laser cut shapes. They were designed for Sun International as gifts for the Sun Star event.
This is a rendering of a housing for a GPS pet tracker. It was part of a series showing off various colour options before going into porduction.
These prototype bottles which I designed for Gulf Energy were 3D printed from ABS plastic on my Dimension1200. A lid pattern was SLA printed for silicon moulding. The batch of lids were then cast in clear blue resin. The lids double as pouring funnels and are designed to be sufficiently complex so as to prevent them from being copied by counterfeit oil resellers.
A rendering of a housing design for an inverter. The housing budget was limited and combines simple sheet metal elements with laser cut acrylic panels. The result is a premium looking enclosure that doesn't break the bank.
These two Mini Coopers were 3D printed from files provided by BMW. Before printing, some time had to be spent carefully thickening the small features in CAD. For example, a 1.2mm steel body panel at 1:1 scale is less than 0.05mm thick at 1:24 scale so the panel needs to be thickened to ensure the scale model is durable enough. Once printed the parts were carefully finished, hand painted and assembled. The two models had to be strong because the were sent to the edge of space as part of a promotion.
These bottle prototypes are CNC milled from acrylic, they are hollow, watertight and can be capped and filled with product because they are made with a production neck finish. This type of prototype is very useful for focus groups and early stage product photograhpy because it is nearly identical to the final product.
This image was carefully constructed in 3D using the bottle manufacturers drawings and the final layers for varnish, foil and other 2D lable details. The combined scene was then carefully lit and rendered.
A themed pen for Sun International. The organic shapes in this design required surface modeling and other CAD trickery. Not forgetting the necesary draft angles and split lines for manufacture. Also, each feature must be correctly constrained to allow seamless changes downstream.